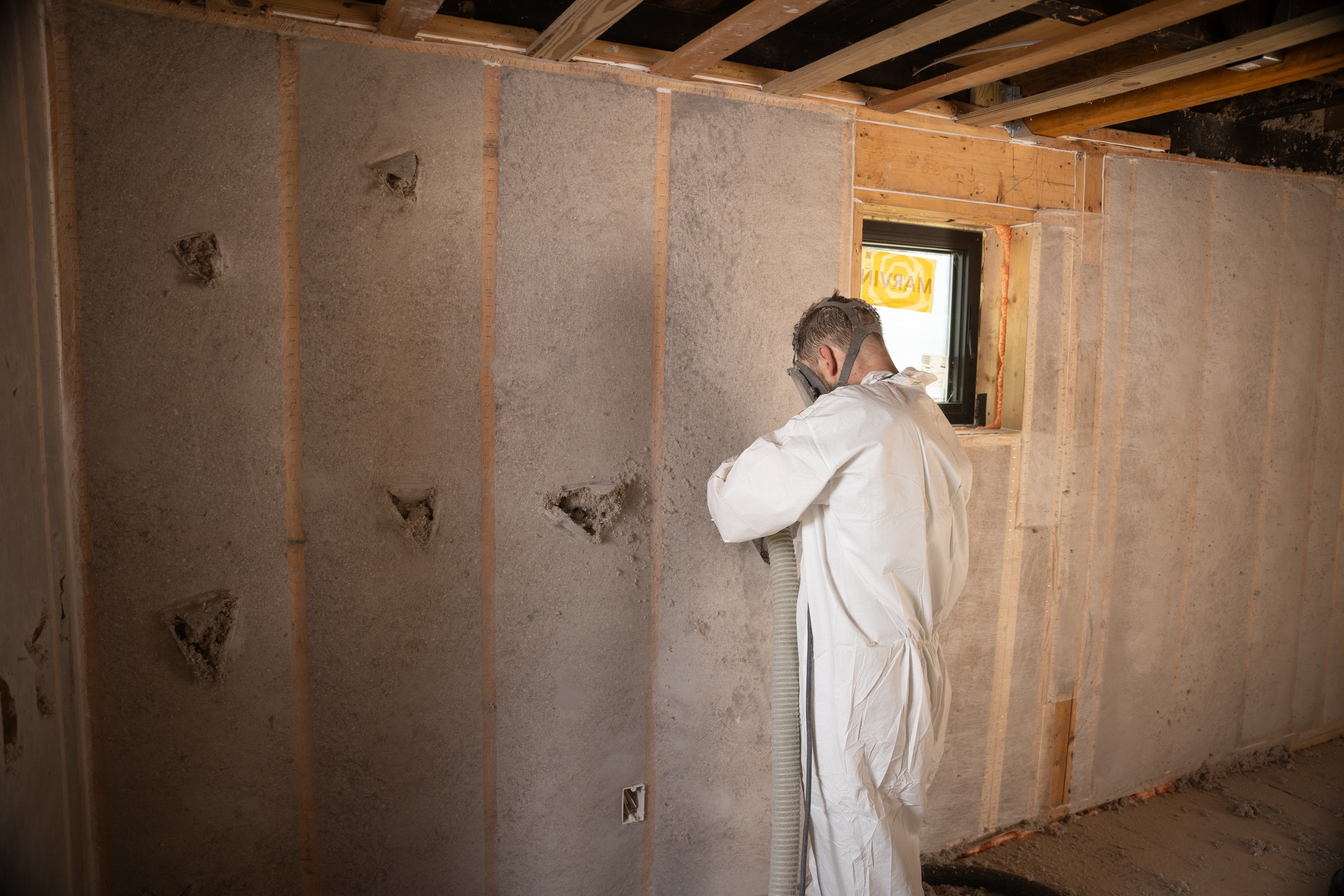
How Greenfiber Insulation Promotes Sustainability in Watauga Community Housing Trust Project
When it comes to home renovations, blending sustainability with preservation is a challenge that demands careful planning. For Rob Howard, president of Howard Building Science and a licensed general contractor, leveraging cellulose insulation for the renovation of a 100-year-old home presented the opportunity to strike that balance.
Led by the Watauga Community Housing Trust, a nonprofit dedicated to creating and maintaining permanently affordable housing in Watauga County, the First Home Fund renovation stands as a prime sustainable housing development example. As a member of WCHT and a long-time advocate for eco-friendly construction, Howard brought his expertise in sustainable building practices to the table, ensuring that the project would not only preserve the home’s heritage but also minimize its environmental impact. Read on to discover how SANCTUARY® by Greenfiber made a difference.
The Watauga Community Housing Trust First Home Fund: A Case Study in Sustainable Housing Development
The renovation was guided by a collaboration between the WCHT and the Junaluska Heritage Association working together to preserve one of the oldest homes in the historic Junaluska neighborhood. WCHT wanted to maintain the home’s historical significance while modernizing it with energy-efficient features that would make it more affordable and environmentally responsible for the future homeowner.
A faculty member at Appalachian State University, Howard decided to use cellulose insulation based on his expertise and involvement with the university’s Department of Energy Solar Decathlon Design Challenge team. The students, who had worked on the design of the renovation, focused on reducing embodied carbon while improving energy efficiency, making cellulose a natural choice for insulation.
“We used this project as the basis of a design for a retrofit project that we submitted to the DOE for the solar decathlon,” Howard said. “The students were tasked with doing a lot of the product research, and to the greatest extent possible, we wanted to specify materials that have a lower carbon impact.”
Challenges and Solutions in Affordable Housing Preservation
Preserving affordable housing can be a challenge in today’s competitive housing market, where the temptation to demolish and redevelop often outweighs the effort to renovate. WCHT highlighted this risk, explaining, “If this home were to sell on the open market, there would be a high likelihood a new buyer would demolish and redevelop the home on the property. This is our chance to help preserve it.” Remarkably, the home withstood the devastating effects of Hurricane Helene, further demonstrating its resilience. By intervening, the organization ensures that this historic home remains a community asset.
Even so, maintaining this historic property came with financial and logistical challenges. Significant repairs were needed, including a reset of the foundation, making fundraising a critical component of the project. Selecting the right materials to balance embodied carbon against operational carbon added another layer of complexity. For example, embodied carbon — the total emissions from material extraction, manufacturing and construction — was a key consideration, alongside operational carbon, or the emissions from heating, cooling and powering the home over time.
“Sometimes it’s easier to rationalize the use of a foam-based insulation if it saves enough energy on the operational side,” Howard said. “However, with cellulose insulation, we got the best of both worlds by using materials with both low embodied and operational carbon.”
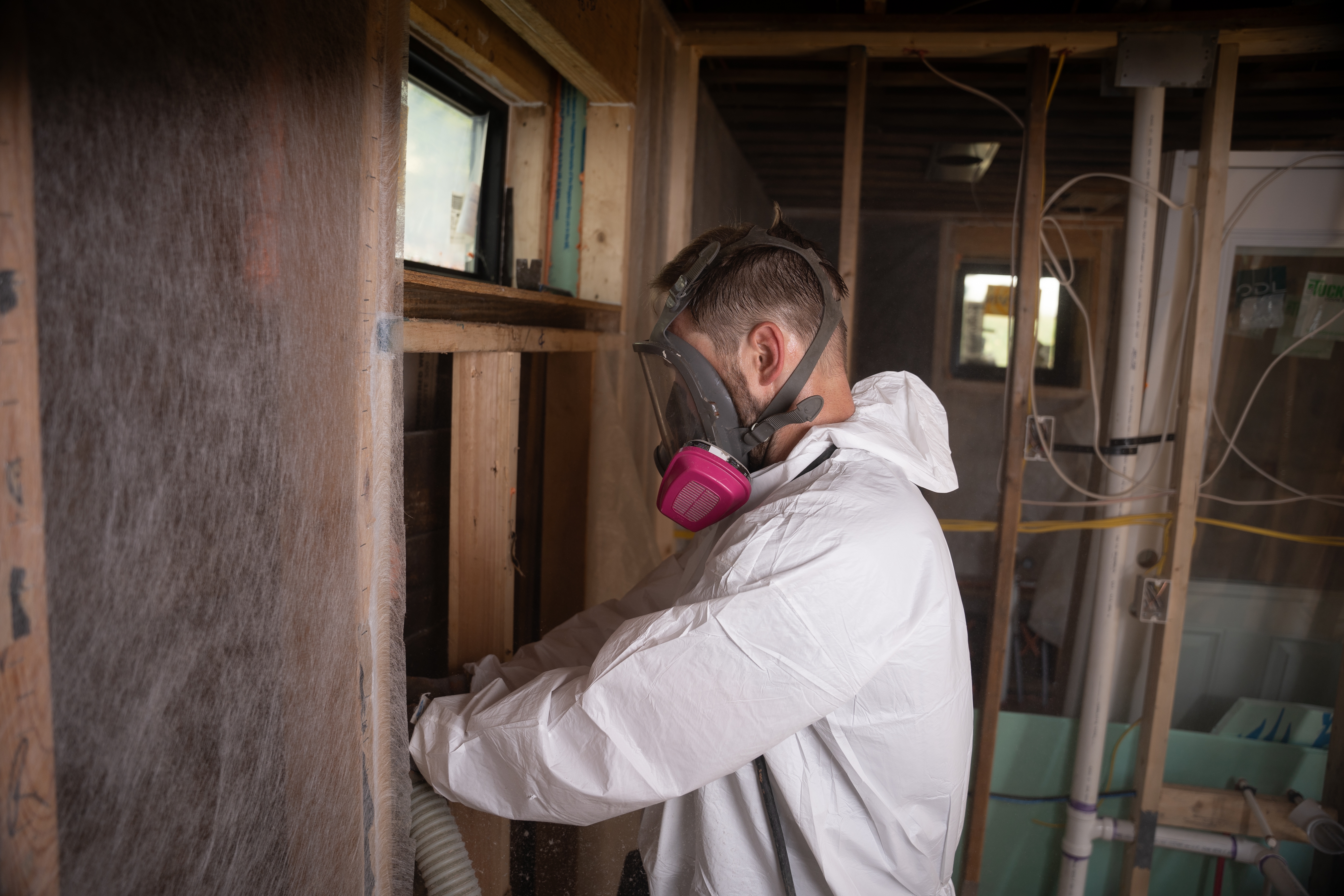
Why Builders Should Choose Greenfiber for Sustainable Housing Projects
For builders committed to sustainability, insulation is more than a performance decision. It’s an environmental one. SANCTUARY delivers on both — it enhances thermal performance, soundproofing and fire resistance as well as overall energy efficiency.
With cellulose insulation, we can isolate carbon in the building instead of releasing it back into the atmosphere. And when installed with the dense-packed method, you’re almost guaranteed a Grade 1 insulation rating because it fills in all the nooks and crannies in the cavity; whereas, fiberglass often leaves gaps, voids and compression — all things we’re trying to avoid. Rob Howard, president of Howard Building Science and general contractor for First Home Fund
Installed in the walls of the Watauga home, cellulose insulation stands out for its ability to provide best-in-class resistance to air infiltration. Dense-packed cellulose completely fills the wall cavity, creating a tight barrier that blocks sound and helps maintain stable indoor temperatures. Unlike traditional insulation materials that often leave gaps or voids, cellulose's high-density packing ensures consistent and effective insulation when properly installed. This thorough coverage reduces the strain on heating and cooling systems and enhances overall energy efficiency.
“With cellulose insulation, we’re able to isolate carbon in the building instead of it being released back into the atmosphere,” Howard said. “When installed with the dense-packed method, you’re almost guaranteed a Grade 1 insulation rating because it fills in all the nooks and crannies in the cavity; whereas, fiberglass often leaves gaps, voids and compression — all things we’re trying to avoid.”
According to the Building Performance Institute’s standard, BPI-104 Envelope Professional Standard for Dense-Pack Wall Insulation Application, dense-packed cellulose at 3.5 pounds per cubic foot qualifies as an air barrier.1 The same study requires alternative materials such as blown fiberglass, mineral wool or spray foam to be installed with specific testing to validate their air resistance. This makes dense-packed cellulose an ideal choice for effective insulation and air sealing.
Furthermore, insulation with a high R-value is fundamental to any energy-efficient or net-zero home, as it reduces heat loss in the winter and heat gain in the summer, which can significantly lower a homeowner’s heating and cooling costs. With a high R-value of 3.7, SANCTUARY excels at reducing heat transfer and improving a home’s energy efficiency.
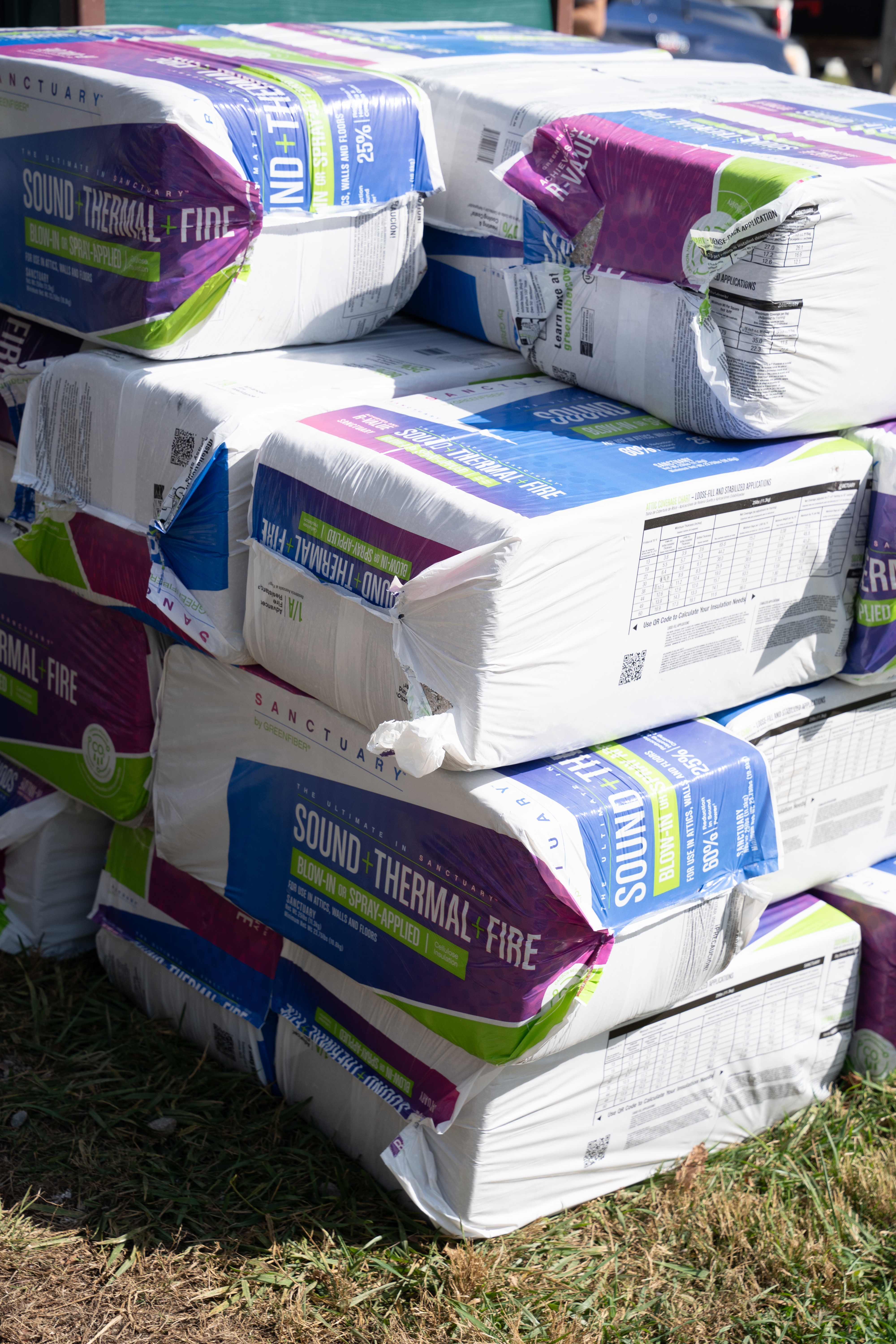
“Ultimately, we want to make sure that homes are comfortable and easy to heat and cool,” Howard said. “They should ideally retain heat in the wintertime and reject heat in the summertime, using as little energy as possible to mitigate these changes.”
In areas like Watauga County, where snowy winters are common, insulation must withstand extreme conditions. SANCTUARY delivers superior thermal performance, keeping homes energy efficient even in the harshest climates.
“To me, I would rather pay a little bit more and know I’m going to get a Grade 1 install and use a more environmentally friendly product than one that hurts the environment but costs less — there’s a lot of benefits and really no cons.”
The First Home Fund serves as a model for affordable housing initiatives that prioritize sustainability. Want to do the same? Fill out the builders and architects form to get more information about how cellulose insulation can benefit your projects, and connect with the Greenfiber sales team to get your hands on the product.
1 BPI-104 Envelope Professional Standard for Dense-Pack Wall Insulation Applications” and by testing for the US Department of Energy as noted in their report “11.4.2 High Impact Project: Support of Standards Development: Dense-Pack Airflow Resistance. Report available upon request.
- Category: Sustainability